Endverpacken
Wie kommt die Kugel in den Karton?
In die herrlich süßen Mozart-Kugeln zu beißen, kann ein wahrer Genuss sein. Damit die Schokoladenspezialität mit dem Kern aus Nougat- und Pistazienmarzipan in den Regalen der Supermärkte zu finden ist, braucht es jedoch erst eine Versand- und Präsentationsverpackung.
Ein Hauch von Schokoladenduft liegt in der Luft – kaum, dass man die Tore zur Produktion von Paul Reber in Bad Reichenhall im Ortsteil Marzoll öffnet. Das Unternehmen stellt die bekannten Reber Mozart-Kugeln im goldenen Stanniolpapier mit dem Porträt von Wolfgang Amadeus Mozart sowie viele weitere feine Schokoladenspezialitäten her. Auf höchstem technischem Niveau werden sie unweit der österreichischen Grenze produziert. Am Anfang der Produktionslinien warten flüssige Schokolade, Marzipan und Nougat, für die weitere Komposition zur echten Reber Mozart-Kugel. Am Ende der Produktionslinie ist eine Endverpackungsmaschine von Somic in Aktion. Die Mozart-Kugeln gelangen in Faltschachteln mit Deckel oder auch als Sideload-Packung zu der Somic 424 DT. Hohe Produktivität am Linienende – bei der Verpackungsmaschine – ist ein Erfolgsfaktor, denn die Kugel-Produktion muss kontinuierlich laufen. Mit der Investition in eine Endverpackungsmaschine ließ sich die bisherige manuelle Kartoniertätigkeit am Ende der Linie automatisieren. Reinhold Kaiser, Betriebsleiter im Werk in Bad Reichenhall, blickt zurück auf die Entscheidungsprozesse: „Wir konzentrieren uns bei jeder Investitionsentscheidung für eine Maschine grundsätzlich auf die Spezialisten. Und Somic ist ein Spezialist im Endverpackungsbereich.“
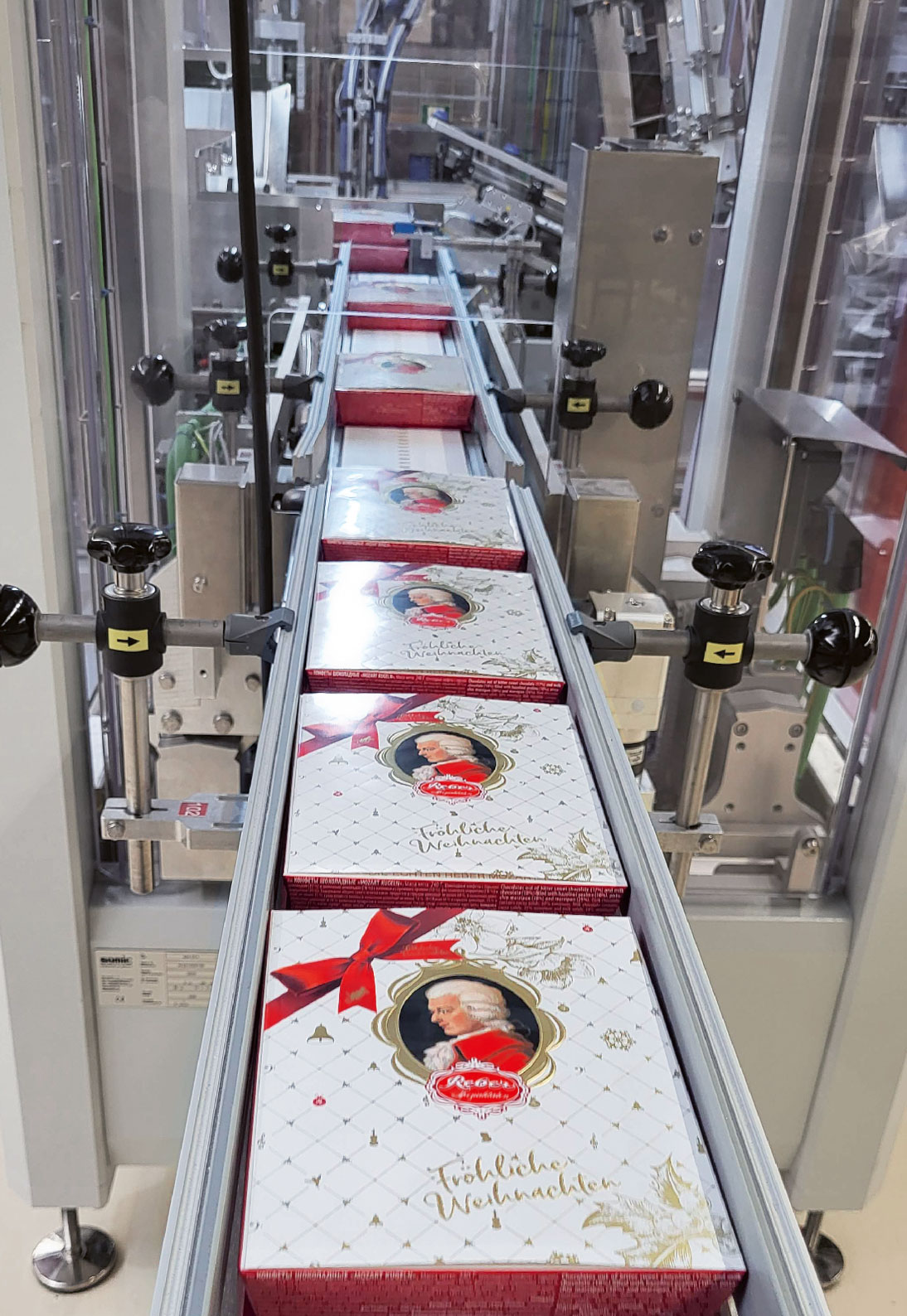
Bilder: Somic
Qualität in neun verschiedenen Kartongrößen
Qualität heißt für das Unternehmen Paul Reber, dass die echten Reber Mozart-Kugeln in ihrer Sekundärverpackung produktschonend gruppiert in den Umkarton gepackt werden. Die Verpackungsmaschine von Somic verpackt je nach Versandeinheit bis zu 100 Packungen pro Minute in die Kartons. Neun verschiedene Kartongrößen verarbeitet die Maschine wahlweise im Tray- oder Deckel-Tray-Format. Der Formatbereich des Produkts zur Verarbeitung in der Maschine reicht in der Länge von 120 bis 260 mm, in der Breite von 100 bis 200 mm sowie in der Höhe von 25 bis 50 mm. Die verarbeiteten Packungen wiegen zwischen 100 und 400 Gramm. Mit dem klassischen Formatsatz inklusive passendem Fächersammler kann Paul Reber zu jeder Verpackungsvariante die gewünschte Produktgruppierung für den definierten Karton einstellen. „Wir haben recht schnell nach der Inbetriebnahme die Verpackungsmaschine im Standardbetrieb nutzen können: Die Mitarbeiter, sowie die Techniker und die Linienverantwortlichen kommen sehr gut mit der Maschine zurecht. Die Formatumstellungen funktionieren schnell und einfach“, so der Betriebsleiter Kaiser.
Stabilität der Kartons erhöht
Vom Mitarbeiterbedarf abgesehen, unterstützte Somic bei weiteren Optimierungen in der Verpackungslinie, denn Reber konnte bei der Projektierung auf den Service des Verpackungsmaschinenherstellers zur Auslegung der Kartonvarianten setzen. „Wir nutzten bisher einen klassischen RSC-Karton, den wir mit Nassklebestreifen verschlossen haben – jetzt arbeiten wir mit einem flachen Zuschnitt“, erklärt Kaiser. Qualitativ hätte man am Kartonmaterial nichts ändern müssen – „wir verwenden nach wie vor eine sogenannte B-Welle.“ Durch die Optimierung des neuen Zuschnitts mithilfe der Somic-Experten, konnten Reber den Materialeinsatz allerdings reduzieren, sodass dadurch erhebliche Einsparungen möglich wurden. Mit dem neuen Kartonkonzept und den Verleimungen im Wraparound-Karton erreicht Paul Reber nun eine höhere Stabilität der Versandkartons. Weitere Einsparungen sind mit der im Maschinenauslauf angedockten Inkjet-Einheit verbunden. „Wir haben bisher alle unsere Umkartons nach dem Verschließen mit Etiketten versehen, die alle notwendigen Informationen für den Versand und die Produktkennzeichnung enthielten. Das haben wir mithilfe des Inkjet-Druckers nun direkt im Auslauf der Verpackungsmaschine gelöst“, erklärt Kaiser. Dies bringe mehrere Vorteile für den Produktionsbetrieb. Etikettendruck: entfällt. Aufkleben des Etiketts: entfällt. Entsorgen des Trägerbands: entfällt. „Wir sparen mehrere Millionen Aufkleber in der Produktion mit der Kombination von Endverpackungsmaschine und Direktbedruckungseinheit,“ so Kaiser.
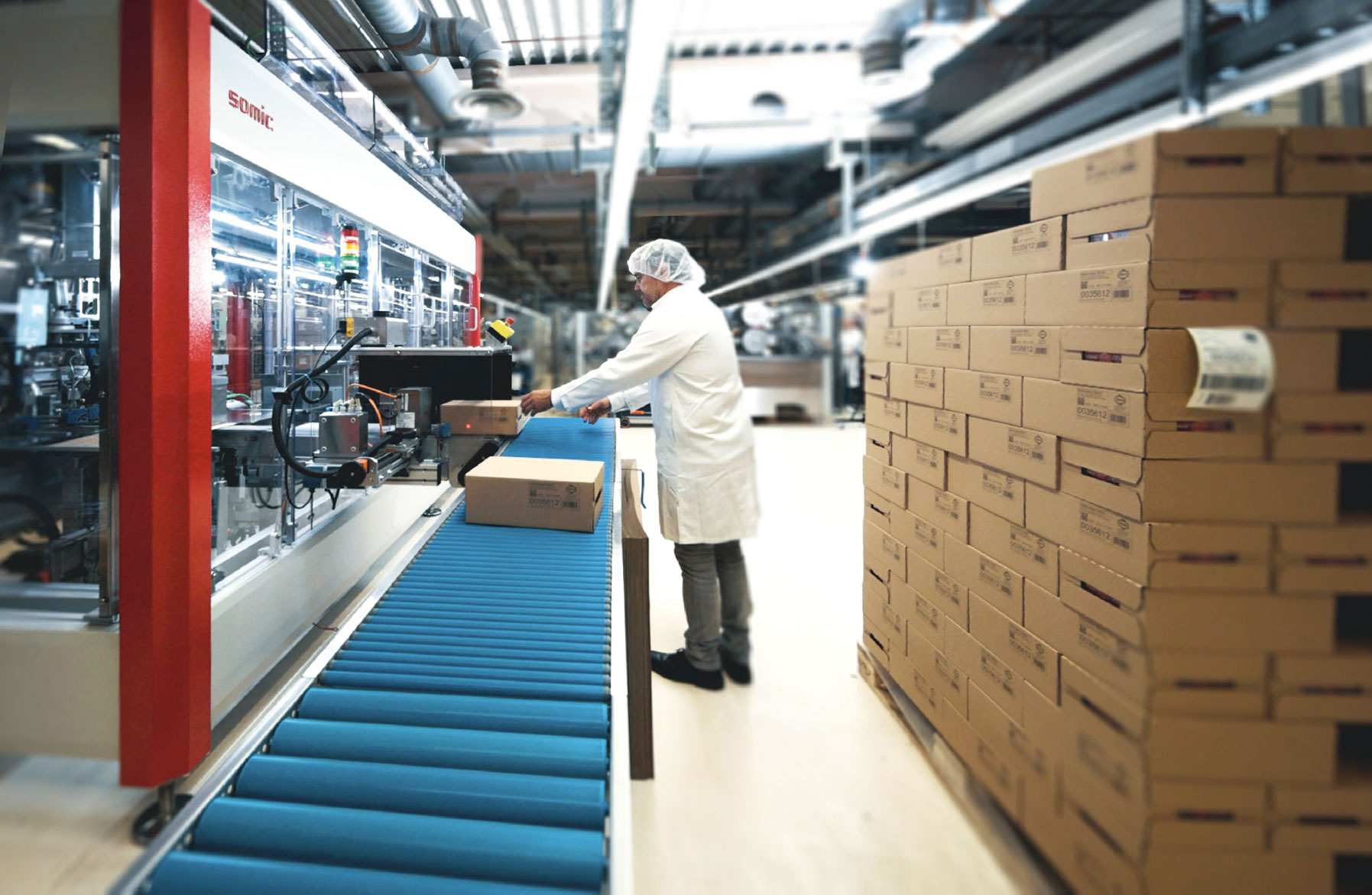
Die Produkte kommen perfekt geschützt und versandfertig aus der Somic Verpackungsmaschine. (Bilder: Somic)
Schnelle Inbetriebnahme
Somic legte mit der Verfahrensweise eines Factory-Acceptance-Tests im Werk in Amerang die Grundlage für eine schnelle Inbetriebnahme. „Innerhalb von zwei Wochen war die Installation in unsere Produktionslinie erledigt und wir konnten sofort in den Standardbetrieb gehen“, blickt Kaiser zurück. Trotz der Pandemie, trotz erschwerter Bedingungen mit Masken, Zugangskontrollen und verschärften Hygienemaßnahmen habe die Installation von A bis Z, bis hin zur Inbetriebnahme und Produktionsbegleitung perfekt funktioniert. Und wie sieht es im laufenden Betrieb aus? Die Verpackungsmaschine wird derzeit im Zweischichtbetrieb verwendet und beweist sich durch ihre robuste Konstruktion. „Wir haben kaum Bedarf an Verschleißteilen und auch die Antriebstechnik funktioniert wunderbar. Im Hinblick auf den Bedarf von Ersatzteilen kommt die DT 424 also gut weg. Das kann gerne so bleiben“, findet Kaiser. Auch die Zielgröße für den Betrieb legt der Betriebsleiter auf den Tisch: „Wir streben einen Wirkungsgrad von 97 Prozent an.“ Derzeit seien sier noch ein paar Prozentpunkte darunter, „aber das hat nichts mit der Endverpackungsmaschine von Somic zu tun“, so Kaiser. Aus der Steuerung der Maschine erhält das Team von Paul Reber Daten wie Stückzahlen, Betriebszustand, Betriebs- und Umbauzeiten oder Störungen und kann diese Daten für die übergreifende Planung nutzen. Kaiser zieht Bilanz: „Wir hatten eine sehr gute Zusammenarbeit vom ersten Kontakt auf einer Messe bis zur Inbetriebnahme in unserem Werk.“ (mns)