Nachhaltigkeit in Unternehmen
Umweltgerecht neu definiert
Im Excellence Centre in Äänekoski, Finnland, arbeit eine große R&D-Abteilung von Metsä Board daran, Kartonqualitäten zu verbessern. (Bild: Metsä Board)
Mit der Packaging and Packaging Waste Regulation (PPWR) ist klar: Unternehmen sind nun gezwungen, nachhaltige Prozesse einzuführen, strenger zu regeln, zu monitoren – und einzuhalten. Viele Unternehmen haben Nachhaltigkeitsstrategien bereits seit Jahren verankert und sind vorbereitet. Vier Unternehmen haben dem packREPORT Einblick in ihren Stand der Dinge gegeben.
Nur so viel Material wie nötig für die jeweils produktspezifische Qualität einbringen und ansonsten auf konstruktive Details setzen – unter diesem Credo fertig das Unternehmen Auer Packaging in Amerang langlebige Kunststoff-Mehrwegverpackungen in Industriequalität, darunter Transport und Lagerbehälter. Einen Lebenszyklus von 15 Jahren und mehr erreicht dadurch ein derart konzipierter Behälter. Am Ende wird er recycelt. Ein Silo auf dem Betriebsgelände ist ausschließlich für Rezyklat reserviert. Rund 2.450 Tonnen recyceltes Kunststoffgranulat verwandelt Auer jährlich in neue Behälter. Ganze Produktgruppen im Sortiment, zum Beispiel Leichtpaletten, Mediumpaletten und Reinraumpaletten, bestehen zu 100 Prozent aus recyceltem Kunststoff. „Meine Zukunftsvision ist eine eigene Recycling-Anlage bei uns im Technologiepark Amerang“, erklärt Sergej Andert, Geschäftsführer, Produktionsleiter und Energiebeauftragter bei Auer. „Momentan scheitert das am Platz. Aber die Zeichen stehen auf Standorterweiterung, wir planen eine vierte Produktionshalle. Vielleicht lässt sich dann auch die Regranulierung vor Ort verwirklichen.“ Die Pläne dafür hat Andert schon in der Schublade. Seit 2015 ist das oberbayerische Unternehmen außerdem nach ISO 50001 zertifiziert und hat sich freiwillig zu einem nachhaltigen Energie- und Ressourcenmanagement verpflichtet. Die selbst gesetzte Messlatte liegt hoch: Neben dem Fokus auf die ressourcenschonende Produktion von recyclebaren Produkten mit langem Lebenszyklus hat die Geschäftsführung Maßnahmen ergriffen, um den ökologischen Fußabdruck kleinzuhalten – vom papierlosen Büro, über regionale Bioprodukte im Betriebsrestaurant bis zur eigens entwickelten, wassersparenden Kühltechnik für die Spritzgussanlagen. Der Plan geht laut Andert auf: Seit Jahren ist in Amerang der CO2-Ausstoß pro Kilogramm Granulat rückläufig. Der Anteil wiederverwerteten Kunststoffs stieg dagegen und liegt derzeit bei 18 Prozent. Das Dach des 2023 in Betrieb genommenen Hochregallagers im Technologiepark Amerang ziert beispielsweise eine neue PV-Anlage. Mit 1,3 Megawatt Leistung versorgt sie das gesamte Betriebsgelände von der Produktion bis zur Verwaltung mit grünem Strom. Wenn die 38 Maschinen am Wochenende stillstehen, wird eingespeist. Beheizt wird der Unternehmenssitz mittels Kraft-Wärme-Kälte-Kopplung. „Heute ist das Wort Wärmepumpe in aller Munde, wir heizen bereits seit 2016 auf diese Methode“, erzählt Andert. Auch die Kühlung der Maschinen sei ressourcenschonend mit einem geschlossenen Wassersystem ausgestattet, bei dem „kein Wasser verschwendet wird“, so Andert. Die Kühlung hat Auer selbst entwickelt. Einmal aufgefüllt, könne das gleiche Wasser bis zu zehn Jahre ohne Zusatz von Chemikalien im Kreislauf bleiben.
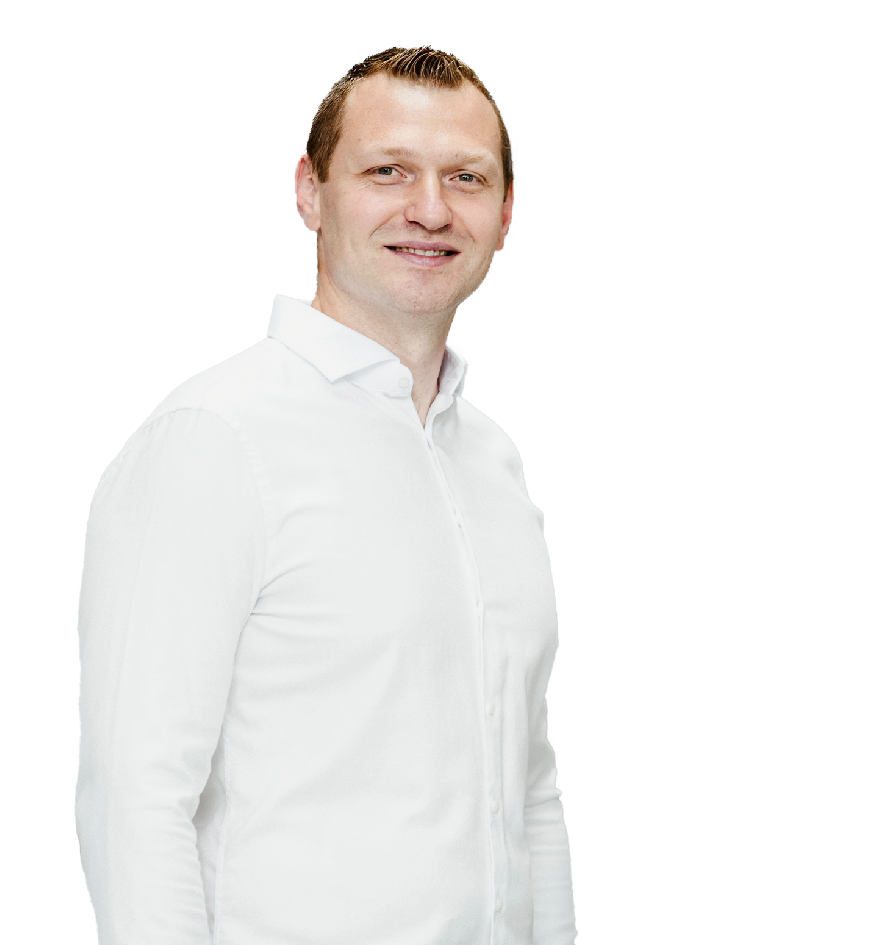
Meine Zukunftsvision ist eine eigene Recycling-Anlage bei uns im Technologiepark Amerang. Die Zeichen stehen auf Standorterweiterung.
Sergej Andert Geschäftsführer, Produktionsleiter und Energiebeauftragter bei Auer
Lightweighting zur Verringerung von Ressourcen
Auch bei dem finnischen Unternehmen Metsä Board ist Nachhaltigkeit das wichtigste Thema, „sie ist sozusagen unsere DNA“, sagt Bernd Gohlke, Account Director bei Metsä Board. Dieser Vergleich scheint Sinn zu ergeben: Denn die Metsä Group befindet sich im Besitz einer Kooperation von Waldbesitzern. Mit großen Zielen: gilt es doch, einen gesunden Wald zu erhalten, der Raum für Erholung bietet, ein Zuhause für Tiere ist, den Wald für die nächste Generation zu bewahren sowie eine nachhaltige Forstwirtschaft zu sichern. Der Anteil an im Unternehmen verwendeter nicht-fossiler Energie liegt laut Gohlke mittlerweile auf einem sehr hohen Niveau. „Derzeit investieren wir in unser Werk in Simpele, Finnland, um die Produktqualität und die Produktionseffizienz weiter zu verbessern und den Kohlenstoff-Fußabdruck unserer Betriebe und Produkte zu reduzieren“, fährt er fort. Ein spannendes Produkt sei vor allem der dispersionsgestrichene Barrierekarton Prime FBB EB mit einer mittleren Barriere gegen Fette und Feuchtigkeit, der gleichzeitig leichtgewichtig ist. Das Lightweighting ermögliche nicht nur einer Verringerung der benötigten Ressourcen – Material, Wasser, Energie – in der Herstellung, sondern verringert laut Gohlke durch ein geringeres Transportgewicht auch den CO2-Fußabdruck über die gesamte Lieferkette. „Durch die Verwendung einer Dispersionsbarriere erreichen wir eine mittlere Fett- und Feuchtigkeitsbarriere, und der Karton kann dabei gleichzeitig gemäß den lokalen Recyclingprogrammen in Papier- oder Kartonabfallströmen recycelt werden“, erklärt der Kundendirektor. Als spannendes Projekt berichtet Gohlke weiterhin von einer LCA-Studie, die durch das IVL Swedish Environmental Research Institute geprüft wurde. Das Ergebnis habe gezeigt, dass die Wahl eines optimierten Frischfaserkartons, den CO2-Fußabdruck von Pharmaverpackungen signifikant senken könne. Insbesondere das Gewicht des Materials sowie die Art der Energie, die für die Produktion verwendet wurden, spielen hier eine große Rolle. „So kann der Wechsel von einem Zellstoffkarton (SBB) zu einem Faltschachtelkarton von Metsä Board den CO2-Fußabdruck der Verpackung um über 50 Prozent reduzieren“, sagt Gohlke. Der Ersatz eines Recyclingkartons (WLC) durch Faltschachtelkarton reduziere CO2-Emissionen sogar um 60 Prozent oder mehr. Neben der Optimierung von Leichtgewichtigkeit erkundet Metsä Board Möglichkeiten, Verpackungslösungen, die aktuell mit Kunststoff arbeiten, durch Kartonlösungen zu ersetzen. „In unserem Excellence Centre in Äänekoski in Finnland haben wir beispielsweise eine große R&D-Abteilung, die daran arbeitet, unsere Kartonqualitäten zu verbessern“, so Gohlke. In gemeinsamen Packaging-Design-Workshops werden dort effiziente Verpackungslösungen sowie Know-how neu- und weiterentwickelt.
Anzeige
Anzeige
PPWR-konform und zukunftsfähig
Mit dem Blick speziell auf PPWR-konforme Verpackungen und zukunftsfähige Verpackungskonzepte gerichtet, arbeiten Entwicklungs-Teams der STI Group aktuell an zahlreichen Projekten. „Die PPWR hat einen Rahmen geschaffen, der die Anforderungen an eine umweltgerechte Verpackung neu definiert“, weiß Jakob Rinninger, CEO der STI Group. Viele Kunden des Familienunternehmens mit Hauptsitz in Lauterbach, Hessen, das auf Verpackungen und Displays aus Karton und Wellpappe spezialisiert ist, würden sich mit der Notwendigkeit konfrontiert sehen, ressourcenschonende Designs zu realisieren. Für zahlreiche Unternehmen habe die STI Group Verpackungskonzepte bereits nachhaltig transformiert und die Recyclingeffizienz gesteigert. Wie bei Metsä Board nimmt auch bei der STI Group das Thema Lightweight eine zentrale Rolle ein. Die Minimierung von Verpackungen hinsichtlich Gewicht und Volumen ist eine zentrale Forderungen der PPWR, beides muss zukünftig auf ein Mindestmaß reduziert werden. Die geforderte Reduzierung birgt laut Rinninger neben Chancen jedoch auch Risiken: Einerseits spare eine ressourcen- und energieeffizientere Produktion Material und schone die Umwelt. Andererseits sei der Grat zwischen zu viel und zu wenig Verpackung sehr schmal und es gelte, das Gleichgewicht zwischen Überdimensionierung und einem ausreichenden Produktschutz zu finden. „Standardlösungen gibt es in diesem Kontext nicht“, resümiert Rinninger. „Allein die Maxime ‚so viel Verpackung wie nötig, so wenig Verpackung wie möglich‘ besitzt für alle Gültigkeit, doch müssen Produkt, Supply Chain und Verwendung immer ganzheitlich betrachtet werden.“ Für eine Minimierung von Gewicht und Volumen setzt die STI Group auf sogenanntes Performance based development, das heißt auf die Verpackungsentwicklung anhand technischer Vorgaben. „Wir zielen darauf ab, effektive und effiziente Verpackungen zu designen, die genau so viel Material in exakt der Grammatur einsetzen, die benötigt wird – nicht mehr und nicht weniger“, so Rinninger. Gleichzeitig setzt das Unternehmen auf besonders leichtgewichtige Materialien, welche nachhaltige und CO2-optimierte Verpackungen mit feineren Wellen sowie deutlich geringeren Grammaturen ermöglichen. Vor dem Hintergrund der neuen PPWR-Gesetzgebung und der damit verbundenen Herausforderungen für zahlreiche Unternehmen, sieht Rinninger auch positive Aspekte und Chancen: „Im Kontext der vielfältigen gesetzlichen Anforderungen, die Balance zwischen adäquater Produktsicherheit, der Vermeidung überflüssiger Verpackungsattribute und einer ansprechender Markenkommunikation zu finden, ist fordernd, aber machbar – und kann ein klarer Wettbewerbsvorteil sein.“
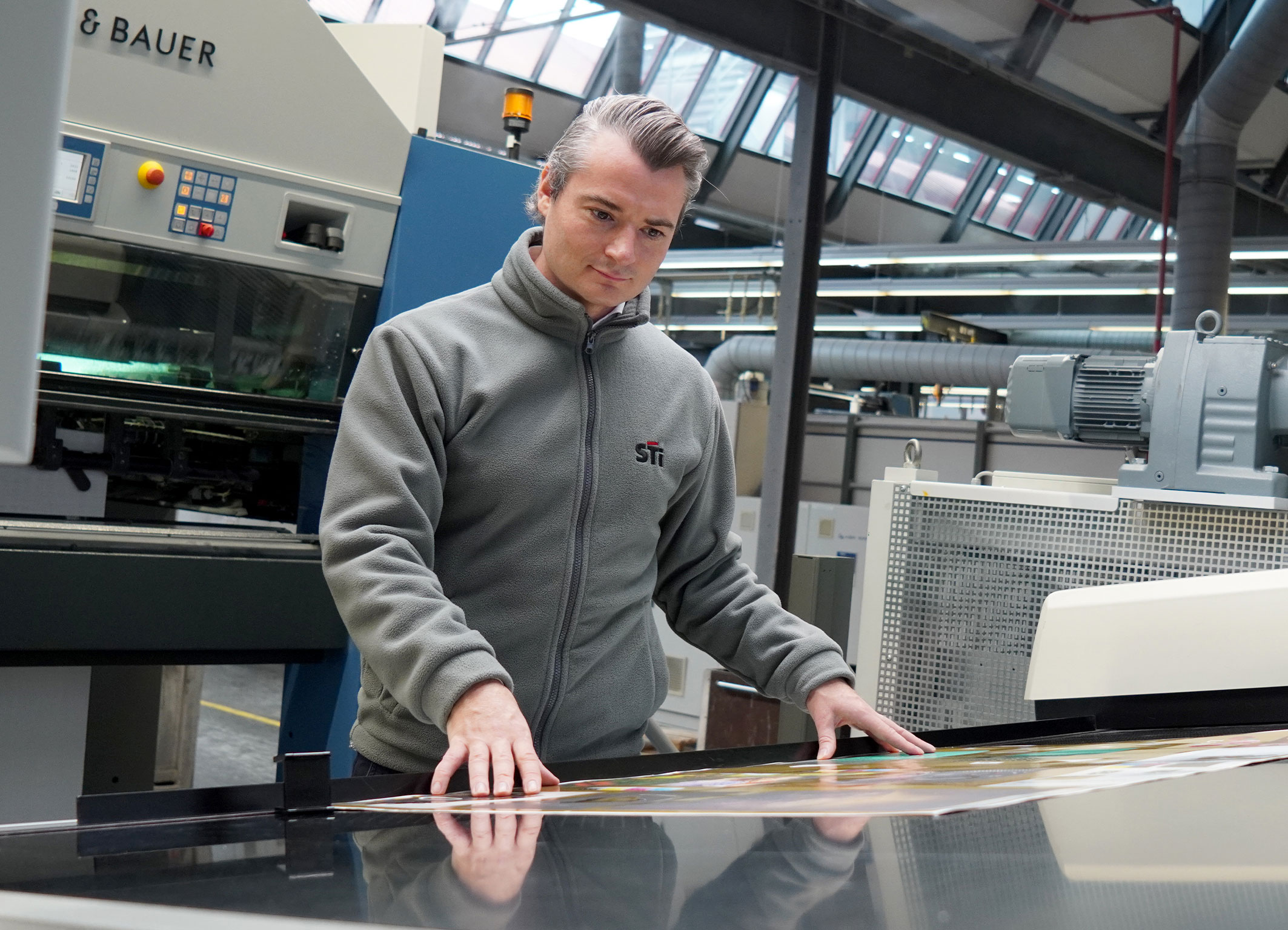
Bei der PPWR-Gesetzgebung sieht STI-Geschäftsführer Jakob Rinninger Herausforderungen, aber auch Chancen: Wer es geschickt angehe, könne Wettbewerbsvorteile erzielen. (Bild: STI-Group)
Weniger Tinten- und Lösungsmittelverbrauch
Was wäre eine Verpackung ohne Kennzeichnung? Wie sich nachhaltige Prozesse bei Tinten und Co. erzielen lassen, zeigt das Unternehmen Leibinger. So steht bei dem Kennzeichnungslösungshersteller die Langlebigkeit von Produkten im Mittelpunkt seiner Nachhaltigkeitsstrategie. Alle Drucker fertigt das Unternehmen am Hauptsitz in Tuttlingen, wo eine Fertigungstiefe von 85 Prozent erreicht wird. Leibinger will Ressourcen damit effizient nutzen und unnötige Transportwege vermeiden. „Im Gegensatz zu vielen Drucksystem-Anbietern auf dem Markt verzichten wir bewusst auf den Austausch kompletter Kernmodule“, erläutert Aljona Barberio, Marketing Manager. „Stattdessen konzentrieren wir uns bei Wartungsarbeiten ausschließlich auf den Austausch einzelner Verschleißteile.“ Dieses Prinzip senke nicht nur die Folgekosten für Unternehmen erheblich, sondern reduziere auch den Ressourcenverbrauch und vermeide unnötigen Abfall. Als Beispiel nennt Barberio den Drucker IQJET, der einen wartungsfreien Betrieb von bis zu fünf Jahren schafft – „weltweit ein Rekord in der Kennzeichnungsbranche“, so Barberio. Tinte und Lösungsmittel sind essenziell für den Druckvorgang, doch ihre Herstellung verbraucht natürliche Ressourcen. Leibinger versucht daher, den Verbrauch dieser Materialien so gering wie möglich zu halten. Zwei zentrale Leibinger-Technologien tragen laut Unternehmen maßgeblich dazu bei: der automatische Düsenverschluss und die Lösungsmittelrückgewinnung. Ein Kernproblem beim Continuous-Inkjet-Druck (CIJ) hat Leibinger so gelöst: Beim CIJ-Verfahren werden schnelltrocknende Tinten verwendet, was einerseits den Vorteil hat, das gekennzeichnete Produkte sofort weiterverarbeitet werden können. Andererseits führt dieser Vorteil bei herkömmlichen Druckern auch zu ihrem größten Nachteil, weil während der Produktionspausen die Tinte im Druckkopf eintrocknet. Die Folge: verstopfte Düsen. Dieses Problem wird in der Praxis durch Reinigungsroutinen beim Starten und Herunterfahren gelöst. Eine technologische Lösung in Form der vollautomatischen Düsenverschlusstechnologie hat Leibinger dafür gefunden. Sie verhindert das Eintrocknen der Tinte vollständig, indem sie die Tinte während Produktionspausen in einem luftdichten Kreislauf verschließt. Dadurch kommt es auch zu keiner Lösungsmittelverdunstung. So entfallen Reinigungen, Unterbrechungen oder Ausfallzeiten. Da weder beim Starten noch beim Herunterfahren des Druckers Reinigungsprozesse notwendig sind, entfällt auch das Hantieren mit Lösungsmitteln, was zur Sicherheit für Mensch und Umwelt beiträgt sowie zu sauberen Produktions- und Verpackungslinien ohne Lösungsmittelrückstände. Die zweite Technologiekomponente zur Einsparung von Ressourcen ist die Lösungsmittelrückgewinnung, die in allen IQJET-Druckern integriert und bei älteren Modellen optional verfügbar ist. „Während des Druckbetriebs wird verdampftes Lösungsmittel aufgefangen und dem System wieder zugeführt. Diese Technologie reduziert den Lösungsmittelverbrauch um bis zu 50 Prozent und sorgt gleichzeitig für niedrigere Emissionen“, erläutert Barberio. „Mit diesen Ansätzen senken wir den Ressourcenverbrauch und unterstützen Unternehmen dabei, nachhaltiger und kosteneffizienter zu produzieren.“ Ist der Unterschied wirklich so groß? Leibinger rechnet vor: IQJET-Drucker verbrauchen 2,7 ml Lösungsmittel pro Stunde. Systeme ohne Lösungsmittelrückgewinnungssysteme verbrauchen laut Leibinger zwischen 6 und 10 ml pro Stunde. Auf einen 3-Schicht-Betrieb mit durchschnittlich 6.000 Gesamtstunden pro Jahr hochgerechnet, lassen sich mit einem IQJET bis zu 43,8 Liter Lösungsmittel pro Jahr einsparen, die sonst in die Umwelt verdampft wären. Bei Tinten selbst setzt Leibinger REACH- und RoHS-konforme Tinten ein sowie spezielle Tintenlösungen, wie beispielsweise MEK-freie Tinten (frei von Methylethylketon) und Tinten mit niedrigem VOC-Gehalt (flüchtige organische Verbindungen). Diese reduzieren die Belastung für die Umwelt. Die Kartuschen, in denen sich die Tinte befindet, sind so entwickelt, dass sie die Tinte bis zum letzten Tropfen entleeren. Im Gegensatz zu Kartuschen, die aus unterschiedlichen Komponenten wie Gehäuse, Innenraum und Deckel aus unterschiedlichen Kunststoffen bestehen, sind Leibinger-Kartuschen zu 100 Prozent recyclingfähig, da sie ausschließlich aus Monomaterial bestehen. (mns)
Der Drucker IQJET erzielt einen wartungsfreien Betrieb von bis zu fünf Jahren, laut Leibinger weltweit ein Rekord in der Kennzeichnungsbranche. (Bild: Leibinger)
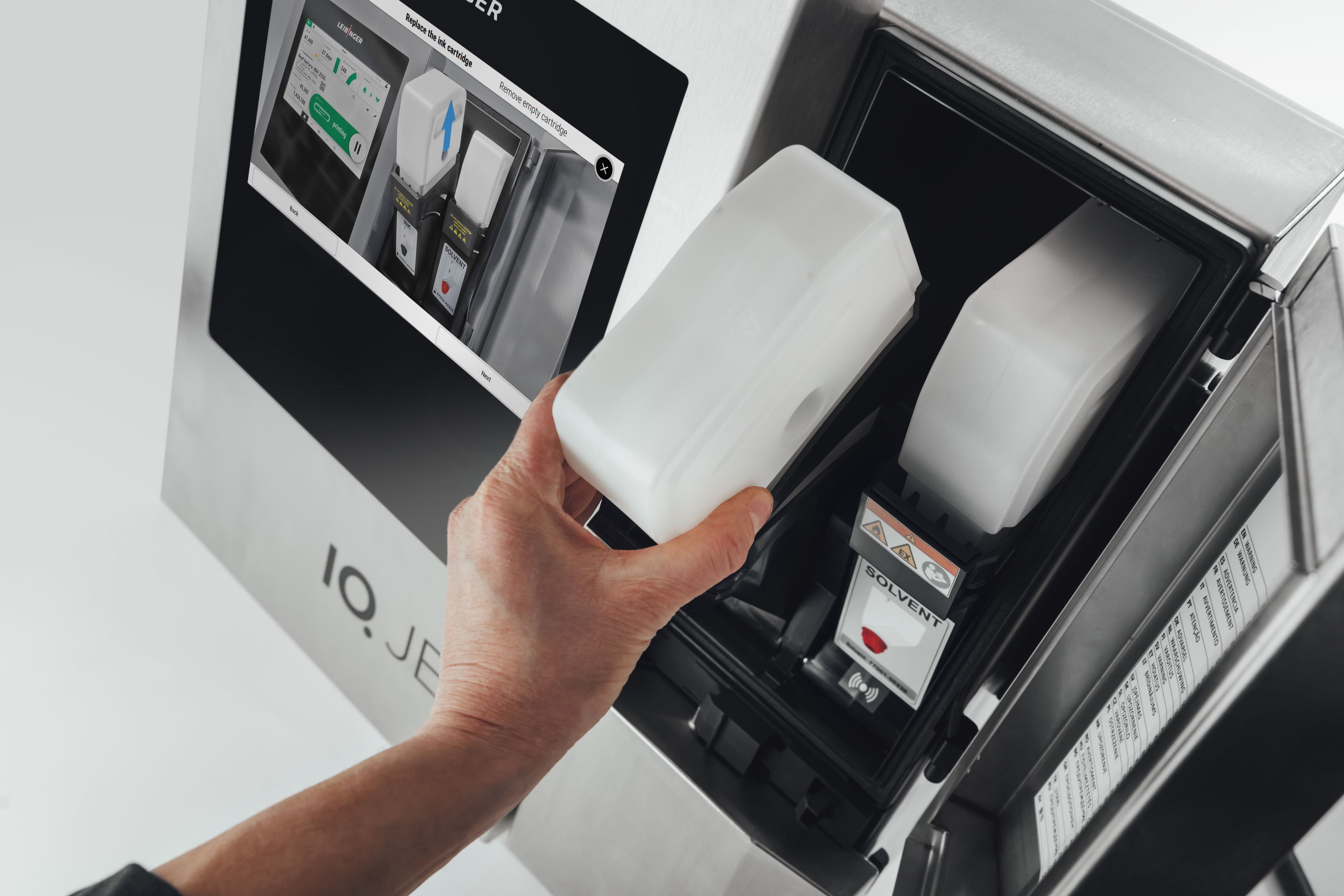